Your Guide to Different Types of Size Reduction Equipment
Size reduction equipment is essential to various industries, from food processing to pharmaceuticals. These machines are pivotal to breaking down solid materials into smaller particles to enable further processing.
Each type of size reduction equipment provides unique capabilities to tackle specific applications and support efficiency. This guide will discuss the different options available and how to select the right one.
What Is Particle Size Reduction Equipment?
Size reduction equipment grinds or crushes materials to reduce their size. The principle of size reduction machinery is to make solid materials into fine particles or smaller pieces, often to increase the material's surface area and improve subsequent processing steps.
For example, this process can enhance product quality, enable easier transport or organization, drive extraction or enable component separation. It is vital for many industries and applications, including food processing, mining, chemical manufacturing, recycling, pharmaceuticals and more.
Each type of size reduction machinery features a specific grinding capacity or throughput while considering factors including desired particle sizes, volume and moisture content.
Generally, these machines use the following primary mechanisms to reduce particle size:
- Compression: Machines with jaw-like components can crush materials between two surfaces.
- Impact: Some equipment uses rotating components to strike raw materials, shattering them into finer particles.
- Shearing: Size reduction equipment can utilize rotating blades or other cutting tools to shear materials.
- Attrition: Rubbing or grinding materials together can reduce particle size through force and friction.
Importance of Size Reduction Equipment
Size reduction equipment is widely used across various industries due to the advantages of leveraging small, more manageable particle sizes. Benefits of size reduction equipment include:
- Improved material handling: Smaller-sized particles empower easier transport and handling, reducing the resources and energy necessary to process materials.
- Faster processing times: Reduced particle sizes allow teams to shorten times in subsequent process steps. For example, extraction, heating and mixing processes can be much more efficient with finer particles.
- Increased surface area: Finer particles have a larger surface area relative to volume, enhancing efficiency and reactivity in chemical processes. Smaller sizes can also lead to quicker dissolution and improved size distribution, often necessary for pharmaceutical applications.
- Uniformity and consistency: Reducing particles into uniform sizes can help ensure product quality throughout manufacturing processes. Additionally, consistent particle sizes can guide predictable performance through compaction, blending and granulation.
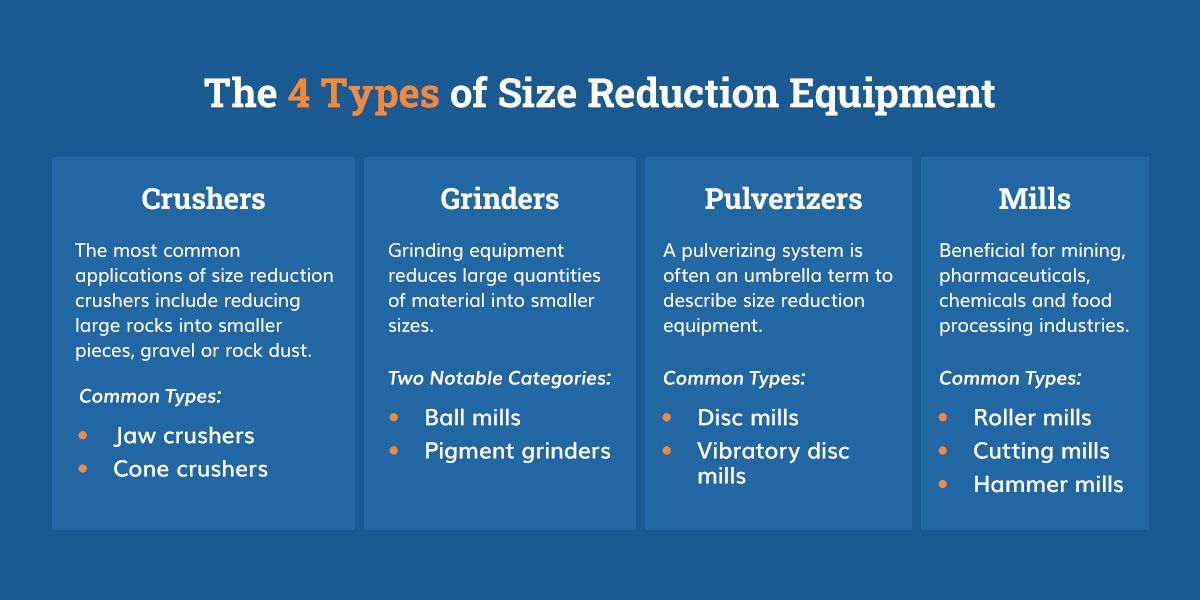
The 4 Types of Size Reduction Equipment
There are four main types of size reduction equipment — crushers, grinders, pulverizers and mills. Below, you can learn more about each option.
1. Impact Crushers
Crushers are among the most popular size reduction equipment. The most common applications of size reduction crushers include reducing large rocks into smaller pieces, gravel or rock dust. These machines can compress or break soft and hard products like limestone, phosphate, gypsum, ore and asphalt. Specific types of crushers include:
- Jaw crushers: This equipment has one stationary and one moving jaw. The moving jaw attaches to an eccentric shaft, allowing it to move up and down. Operators can adjust the jaw movement and gape to suit the material they feed into the machine and their desired output.
- Cone crushers: Cone crushers are ideal for reducing the size of medium to very hard materials. This equipment is common in mining applications using copper and iron ore. Road construction teams can also use these machines to crush building materials like asphalt and concrete.
2. Industrial Grinding Machines
Grinding equipment reduces large quantities of material into smaller sizes. It differs from crushers in several ways. Grinders can create finer, more uniform particles, while crushers turn materials into more manageable pieces. Additionally, grinders are often more suitable for softer materials, such as plastics, chemicals and grains, while crushers can handle harder materials like rocks and minerals.
Grinding equipment is common for several applications, such as grinding grains, milling coal and producing powders. Common types of grinding machines include:
- Ball mills: Ball mills can handle large materials. This equipment relies on rotation speed, ball size and material type to create smaller particles. Industries that commonly use this equipment include pharmaceuticals, ceramics, mining and paint manufacturing.
- Pigment grinders: Pigment grinding machines make milling processes and pigment refinement possible. This equipment is common in the cosmetics, plastics, pharmaceuticals, paint and food industries where food or product colors are essential.
3. Pulverizers
A pulverizing system is often an umbrella term to describe size reduction equipment. This broad category encompasses impact mills, crushers and grinding mills. Two notable categories of pulverizers include:
- Disc mills: This equipment uses two horizontal discs to grind materials. One disc is stationary, while the other rotates. As operators feed material into the machine, compression and mechanical shearing reduce particle size.
- Vibratory disc mills: Vibratory disc mills can grind dry materials into fine particles and powders. These machines use high-frequency vibrations to achieve fine grinding. Some machines offer adjustable vibration frequencies to optimize grinding performance.
4. Mills
Mill machines pulverize materials in multiple ways. This equipment is beneficial for mining, pharmaceuticals, chemicals and food processing industries. Common types to note include:
- Roller mills: This equipment features two or more cylindrical rollers that grind and crush materials as they rotate. Common applications for these mills include producing powdered minerals and milling grains like corn and wheat.
- Cutting mills: Cutting mills are common in the food industry and for applications needing to cut soft to medium-hard materials. These machines often feature cutting plates and a high-speed rotor for size reduction.
- Hammer mills: There are several types of hammer mills, including lump breakers, full circle, gravity discharge, pneumatic discharge and horizontal in-feed hammer mills. Generally, this type of equipment is suitable for food product grinding, recycling and scrapping, powder production, dissolution and energy source reduction.
Choosing the Right Equipment
While each type of pulverization equipment can reduce particle size, finding the right machine for your specific operations is crucial. Consider these factors when deciding which equipment is right for your applications:
- Material type: One of your first considerations should be material type. Different machines are suitable for materials of varying toughness. Consider whether you are working with soft or hard materials to narrow your search.
- Desired particle size: Particle size distribution is another important element because some equipment can make more uniform particles than others. Additionally, smaller particles are often more manageable to work with and can quicken other processes, so understand your size needs.
- Production volume: Production volume is crucial because this metric will provide insights into metrics like capacity requirements and operational efficiency. Additionally, choosing equipment that scales up or down to suit your business needs is important.
- Manufacturer: The equipment manufacturer should also play a part in your decision. Consulting with manufacturers like Pulva for expert advice can help you find the right machine and ensure you have the support you need to overcome challenges and optimize operational efficiency.
Find Quality Pulverizing Equipment From Pulva Corporation
For nearly 80 years, our mission at Pulva has been to provide quality equipment and services to industries needing particle size reduction. Our complete line of pulverizing milling solutions empowers businesses across industries to complete operations efficiently.
With ultramodern manufacturing equipment, knowledgeable team members and state-of-the-art facilities, you can rely on us to find lasting solutions and deliver exceptional support. Connect with a member of the Pulva team to learn more about our tailored recommendations for your business.