Benefits of Cryogenic Grinding
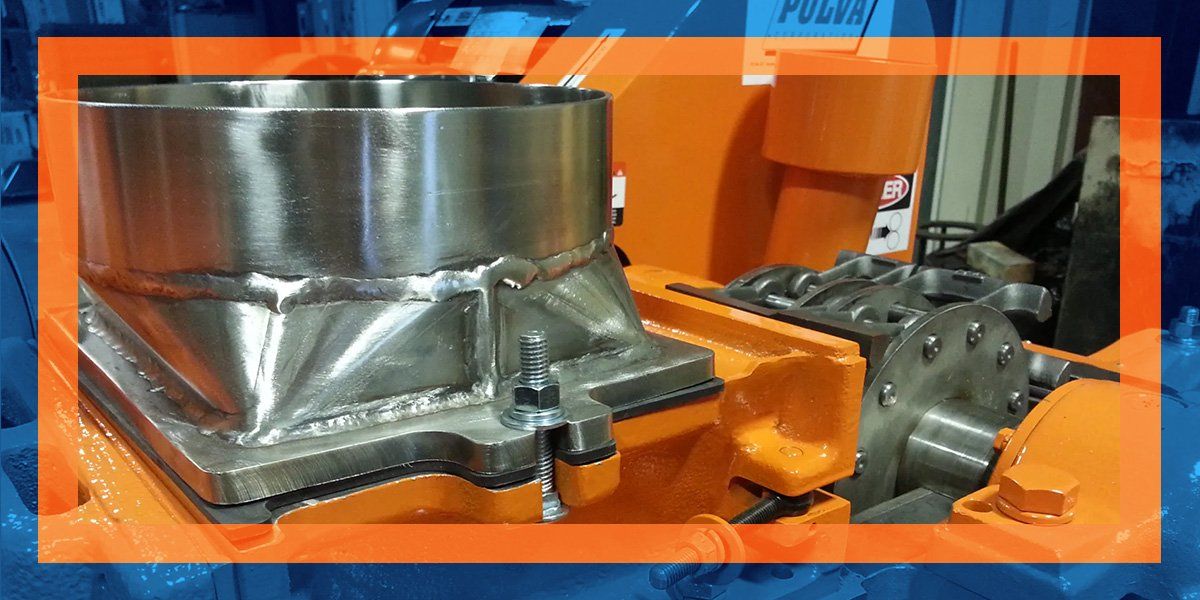
Cryogenic grinding has become popular across multiple industries due to the myriad of benefits the process offers. Cryogenic feeders help you grind sensitive materials, achieve uniform particle distribution and increase production rate without compromising product quality. Below, learn what cryogenic grinding is and its step-by-step process to help you understand how it works and how you can apply it.
Cryogenic grinding is the process of chilling or cooling materials and reducing them to smaller particles before formulating or mixing them. In other words, the material is cooled and embrittled using extremely cold nitrogen and then crushed, resulting in fine particles with the same product quality as the original.
The cryogenic grinding process has many names, including freezer milling, freezer grinding, cold grinding and cryogenic milling (cryomilling). Cryogenics is one of three toll grinding techniques — dry and wet grinding being the other two. Cryogenic grinding is unique because it is reserved for situations where the materials cannot be reduced by dry or wet milling. The addition of liquid nitrogen simplifies the grinding process, making it easier to reduce the materials.
For example, grinding thermoplastics at ambient temperatures poses significant challenges because they soften, clog screens and adhere in lumpy masses. Similarly, friction makes crystalline materials melt when ground without cooling. Chilling them helps you grind them efficiently into refined grains and enhances their applications.
Cryogenic grinding also enables accurate particle size distribution (PSD), which is vital to manufacturers across various industries. Here are three examples:
- Regulatory compliance: Manufacturers rely on PSD measurements to determine compliance with regulations and industry standards. For example, the International Conference on Harmonization guidelines note when to consider particle sizes.
- Production improvement: Analyzing particle size distribution can uncover ways to improve the production process. The reason is PSD can affect the new product's safety, efficacy, shelf life and manufacturability.
- Contamination status: Manufacturers often assess PSD to determine whether the product is free from contaminants. It also helps you identify the possible sources of the contamination without compromising product quality, therefore improving quality control.
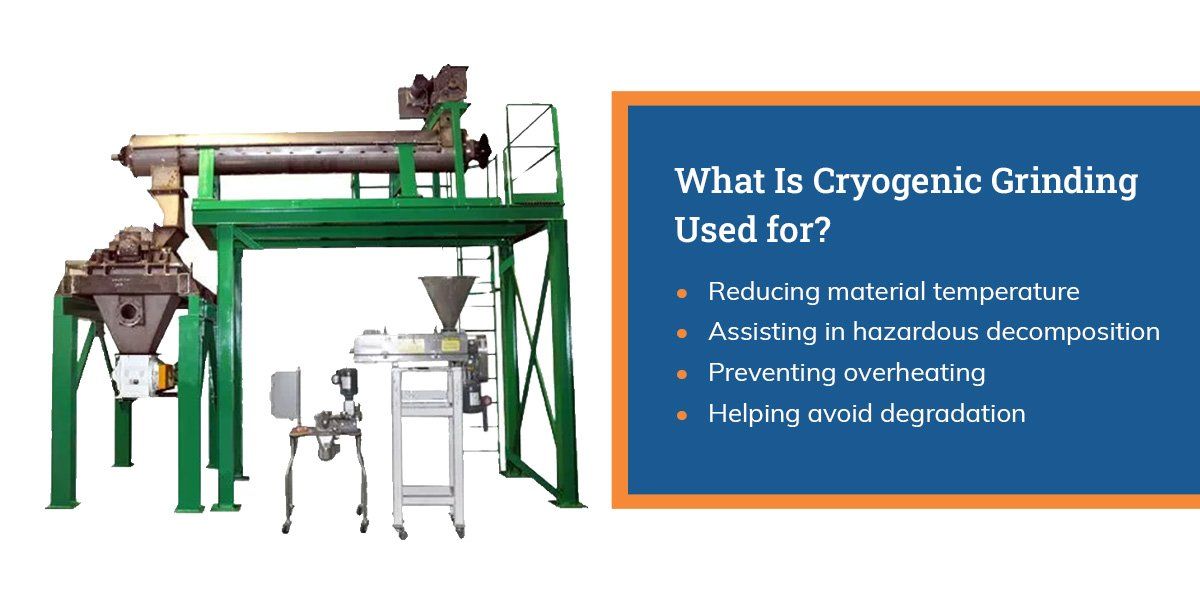
You can use cryogenic grinding for the following:
- Reducing material temperature: Materials below their glass transition temperatures are broadly friable to some degree. Cryogenic grinding helps reduce the material temperature below the glass transition temperature — the point at which a polymer transforms from a glassy, brittle state at low temperatures to a rubbery, elastic form at high temperatures.
- Assisting in hazardous decomposition: The process is used in temperature control, which helps prevent hazardous decomposition in the mill's high-energy environment.
- Preventing overheating: Materials that are hard to mill generate heat during the milling process. For materials to be friable, they must stay below their softening points or melt temperatures. Freezer grinding keeps material and mill from overheating.
- Helping avoid degradation: Cryomilling assists in oxygen exclusion and prevents the milled materials from degrading when new surfaces are formed.
Cryogenic grinding is one of the finest methods of material reduction. So, how do cryogenic feeders work? Here is a step-by-step explanation:
- The material is cleaned and fed into the hopper.
- The material exits the hopper and enters the vibratory feeder, which is inclined towards the helical screw conveyor's entry point. This step helps you control the speed rate.
- Liquid nitrogen is released from the storage container and sprayed into the cooling screw conveyor and onto the material at -320 degrees Fahrenheit.
- The liquid nitrogen absorbs the required heat from the feed material and vaporizes.
- The cold nitrogen gas continuously cools the material and embrittles it as it seeks thermal equilibrium.
- Additional liquid nitrogen may be injected into the grinder to remove heat. A temperature controller and thermocouple are used to monitor and control the temperature within the conveyor.
The benefits of cryogenic size reduction are numerous:
- Prevents caking: Cryogenic feeds safeguard temperature-sensitive materials against thermal deterioration. This process eliminates the risk of product caking in the mill.
- Creates ultra-fine particular grinding: Compared to traditional milling methods, cryomilling produces finer ground particles. With a particle size of 10 micrometers or smaller, cryomilling improves polymers' particle flow and dispersion potential for processed polymers and foodstuffs in liquid.
- Helps grind sensitive materials: Some materials are temperature-sensitive and challenging to hone. Liquid nitrogen cooling eases the process and improves grinding efficiency.
- Increases production rate: Cryogenic milling optimizes the particle size and makes them easier to process. This reduces production times and ensures maximum output by increasing the particle yield.
- Offers uniform particle distribution: Cryomilling generates ultra-fine particles within narrow distribution ranges. With the customizable sieving system, you can evenly categorize materials to ensure maximum yield, stability and improved product performance.
- Preserves product quality: A primary advantage of using cryogenic grinding is it reduces the product size to the required measures without affecting the quality. This is important across various industries, especially food and aquatic products. The process prevents thermal degradation throughout, thereby retaining the needed standard.
- Improves safety: Cryogenic grinding makes the grinding process safer. The feeders create an inert environment that protects against oxidation and fire, improving operational safety.
- Eliminates thermal degradation: Cryogenic grinding helps you handle the temperature management challenges associated with industrial grinding. The cryogenic process embrittles the materials, allowing them to fracture instead of bending, melting or deforming. This process makes the method attractive to manufacturers across industries.
Cryogenic grinding is applied in multiple industries, including the following:
- Food processing: Manufacturers within the food processing industry rely on cold grinding to optimize operations by reducing raw materials and products into particulate form. Cryogenic feeders are perfect for cooling down sugary and fatty food items with high-temperature sensitivity, such as cheese, dried fruits and oily spices, while maintaining the flavor.
- Manufacturing: Carbon black is a crucial product in manufacturing plastics, rubbers, pigments and coatings. With cryogenic feeders, you can pulverize carbon black without thermal degradation.
- Steel grinding: The grinding process generates excessive heat at high speed and feeds rate, drastically raising the temperature at cutting zones. Providing liquid nitrogen to the grinding spot allows you to overcome this challenge.
- Recycling: Recycling is one of the most crucial industries today, and cryogenic grinding plays a vital role in the process. Cryogenic feed attachments are efficient for crushing recyclable materials such as bottles, glass, tires, leather and plastics and preparing them for reuse.
- Pharmaceuticals: Pulverizing powders for pharmaceuticals is a straightforward and efficient way to improve pharmacological properties. Cryogenic milling also prevents temperature-sensitive material from thermal degradation and preservers its efficacy.
Some other typical applications are:
- Waxes
- Adhesives
- Rubber
- Thermoplastics and thermosets
- Plastics
- Resin
- Composites
- Biological samples
- Coatings
- Explosives
Cryogenic grinding offers numerous grinding solutions. The cryogenic grinding process helps you achieve ultra-fine particular grinding, increases production rates and eliminates thermal degradation while maintaining product quality. Investing in high-quality cryogenic grinding equipment also offers added benefits, streamlining your operations and increasing your return on investment.
Pulva Corporation is a leading provider of quality size reduction equipment that helps customers with their size reduction needs. With over 80 years of experience in the industry, we understand your needs and are ready to partner with you. Contact us today to learn more about our products and services and how we can help you achieve a personalized solution.