Hammer Mill Maintenance Guide
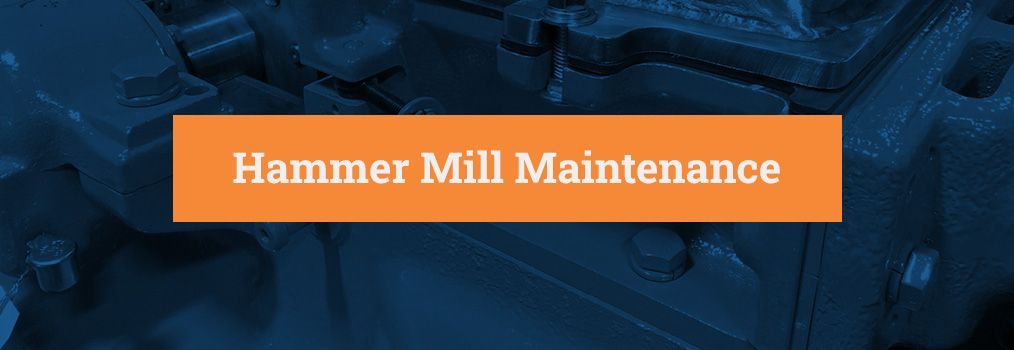
Hammer mills are used in various manufacturing processes to grind products into different feeds, such as those used for pets and livestock, or for grinding or processing seeds into oils, among other applications. Regardless of what a hammer mill is used for, it must be adequately maintained. Proper sizing and operation can help reduce maintenance costs and requirements, but maintenance is still required to maximize the efficiency of your hammer mill.
In our hammer mill maintenance guide, you will learn more about upkeep for these machines, including what regular and long-term maintenance tasks are required to keep your hammer mill in the best condition possible.
Performing routine hammer mill maintenance is easier than repairing extensive damage due to insufficient care. Hammer mills undergo a lot of wear and tear during grinding, so regular maintenance is essential to reduce the risk of component damage or unexpected breakdowns. Routine maintenance and inspections ensure that your hammer mill components are in the best condition to provide a long service life.
Anyone performing hammer mill maintenance should know how to care for and replace the essential components. You can ensure your business keeps up with machine care routines by creating a list of maintenance tasks and a schedule for employees to follow. Making a list of tasks ensures that hammer mill maintenance is not forgotten, minimizing the risk of unexpected and costly downtime.
If you are using a hammer mill for your operations, you must keep up with regular component inspections and replacements. Any moving or rotating components should be regularly inspected since they will wear faster than stationary parts and can affect overall performance.
You can prevent downtime by having different components on hand in case they need replacements. Some of the components you should keep include:
- Hammers
- Hammer rods
- Screens
- Bar grates
- Wear plates
- Bearings
Since you are working with moving parts, you will also want to stay on top of lubrication. Lubricating moving components will help reduce premature wear and tear and lower replacement frequency. You should also check airflow to ensure ground materials do not sit in the mill for prolonged periods.
On top of component inspections and replacements, you will also need to keep up with long-term maintenance items such as the following:
Flow Directors
Flow directors help ensure that materials are guided into the path of the hammers. Circulating materials can cause abrasions to the back side of the flow directors, which will cause them to wear down and eventually require replacement. Generally, flow directors need to be changed once every 18 to 48 months, depending on your exact applications and frequency of use, to prevent catastrophic failures.
Bearings
Bearings need maintenance to ensure they can continue to provide reliable service. While lubrication is critical for many bearings, hammer mill bearings have the potential to become over-lubricated. You should check your bearings once every six to 12 months to clean out old grease and prevent over-lubrication. The new bearings should only be packed up to half full with new grease and monitored carefully for the following 12 hours.
Screen Carriages
Screen carriages can experience wear and impact, causing the component to lose its form. Worn screen carriages can become problematic, especially in hammer mills used for grinding pet food or involved in aquaculture feed applications. You will want to inspect the screen carriages regularly to check for signs of wear and tear. If a screen carriage has become damaged over time, you should replace the screens to help maintain the machine's performance and reduce the risk of leaks.
Wear Liners
Wear liners in the interior of the hammer mill help create an effective seal, but they are also prone to abrasion and damage as the hammer mill operates. Though they are the longest-lasting option, even wear liners made from abrasion-resistant steel can be prone to damage after some time. You will want to keep an eye on the wear liners inside your hammer mill and replace them when you notice signs of damage that could affect the seal.
Motor Coupling
The motor coupling becomes stressed and flexed whenever you start the machine. A misaligned motor coupling can also cause the hammer mill to vibrate, resulting in unexpected damage. You should check the motor coupling and its alignment at least once every six to 12 months to ensure the elements are sound and the mounting and coupling bolts are fastened tightly.
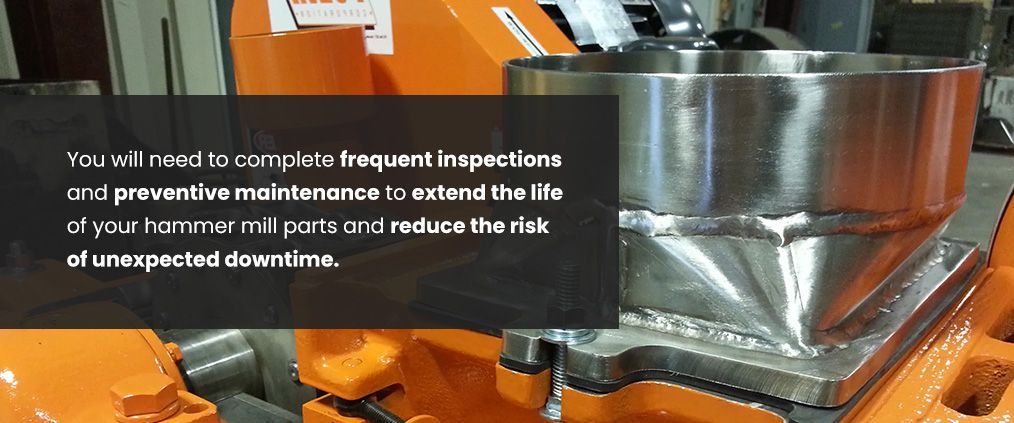
You will need to complete frequent inspections and preventive maintenance to extend the life of your hammer mill parts and reduce the risk of unexpected downtime. Components will become worn over time, and failing to replace them in time can result in costly damage to your equipment.
Having components on hand is essential to ensuring you can replace them as needed. Use the following information to determine when you need to inspect and replace different components for your hammer mill.
Hammers
Hammer mill hammers can either be two-way or four-way reversible. The hammer type will indicate how many rotations the part is capable of before it needs to be replaced. Eventually, the cutting edge of the hammer will become rounded, affecting the machine's efficiency. Hammer mill hammers should be replaced when the cutting edges become rounded.
Hammer Rods
Hammer rods are directly involved with the hammers and should be inspected anytime you need to replace or rotate the hammers. With use, hammer rods can become grooved, impacting your machine's overall performance. When you inspect the hammers and hammer rods, look for any signs of grooving and replace the component when necessary.
Screens and Bar Grates
Screen or bar grates help you achieve the desired particle size for your manufacturing process. If your screens or bar grates are not working correctly, it could lead to undesirable particle sizes. You should inspect and replace these parts if the perforations have become elongated or rounded.
Wear Plates
Wear plates are used to prevent damage in hammer mills that process abrasive or hard materials, extending the life of the equipment. When examining the wear plates, be sure to check their thickness to determine if they are thinning, which would indicate that they need to be replaced. You can check for early signs of this issue by looking at bolts, which will develop extra space between them and the component if the wear plates are thinning.
Bearings
Your hammer mill's bearings help carry the motor's load but will eventually wear out over time. Generally, you want to replace the bearings in pairs, but you may need to replace more if the damage is significant. When you conduct your inspection, you will want to check your bearings for signs of excessive heat, vibrations, spinning or squeaking. These signs indicate that the bearing needs to be replaced.
Hammer mills are essential to size-reduction processes across different industries and must be maintained to reduce the risk of costly downtime. Pulva's team of size-reduction equipment experts can help by providing industry knowledge, quality equipment solutions, and services and parts.
We have over 80 years of experience delivering quality to our clients. Our team can help you with everything from fabrication capabilities to replacement components, regardless of what you need. Request a quote from us today to get started!